Lab Companion-Rapid Temperature Cycling Test Chamber
Introduction of Lab Companion
With over 20 years of experience, Lab Companion is a world class manufacturer of environmental chambers and an accomplished supplier of turn-key test systems and equipment. All our chambers build on Lab Companion’s reputation for long life and exceptional reliability.
With a scope of design, manufacture and service, Lab Companion has established a quality management system that complies with the International Quality System Standard ISO 9001:2008. Lab Companion’s equipment calibration program is accredited to the International Standard ISO 17025 and the American National Standard ANSI/NCSL-Z-540-1 by A2LA. A2LA is a full member and signatory of the International Laboratory Accreditation Cooperation (ILAC), the Asia Pacific Laboratory Accreditation (APLAC) and the European Cooperation for Accreditation (EA).
Lab Companion’s SE-Series Environmental Test Chambers offer a significantly enhanced airflow system, which provides better gradients and improved product temperature change rates. These chambers utilize Thermotron’s flagship 8800 Programmer/Controller featuring a high resolution 12.1” flat panel display with touch screen user interface, expanded capabilities to graph, data log, edit, access on-screen help, and long term hard drive data storage.
Not only do we offer the highest quality products, we also provide ongoing support designed to keep you up and running long after the initial sale. We provide factory direct local service with an extensive inventory of the parts you might need.
Performance
Temperature range: -70°C to +180°C
Performance: With 23 Kg aluminum load (IEC60068-3-5), the rising rate from +85°C to -40°C is 15℃/min; the cooling rate from -40°C to +85°C is15℃/min too.
Temperature control:± 1°C Dry bulb temperatures from control point after stabilization at the control sensor
Performance is based on an ambient condition of 75°F (23.9°C) and 50% RH
Cooling/Heating Performance based on measurement at the control sensor in the supply air stream
Constructure
Interior
Nonmagnetic Series 300 stainless steel with a high nickel content
Internal seams heliarc welded for hermetic sealing of the liner
Corners and seams designed to allow for expansion and contraction under the temperature extremes encountered
Condensate drain located in the liner floor and under the conditioning plenum
Chamber base is fully welded
“Ultra-Lite” non-settling fiberglass insulation
One adjustable interior stainless steel shelf is standard
Exterior
Die-formed treated sheet steel
Metal access covers provided for easy opening doors to electrical components
Finish water-based, air dry lacquer, sprayed over a cleaned and primed surface
Easy lift-off hinged access doors for servicing the refrigeration system
One 12.5 cm diameter access port with interior weld and removable insulating plug mounted in right hand side wall accessories on hinged door for easy access
Features
Chamber Operation clearly displays helpful run-time information
Graphing Screen offers expanded capabilities, enhanced programming and reporting
System Status displays crucial refrigeration system parameters
Program Entry makes it easy to load, view and edit profiles
Set Up quick-step wizards make profile entry easy
Pop-up Refrigeration Charts for handy reference
Therm-Alarm® provides over & under temperature alarm protection
Activity Log Screen provides comprehensive equipment history
Web Server allows internet access to equipment via Ethernet
User-Friendly Pop-up Key Pad makes data entry quick and easy
Includes:
- Four USB Ports-two External & two Internal
- Ethernet
- RS-232
Technical specifications
1-4 independently programmable channels
Measuring Accuracy: 0.25% of span typical
Selectable °C or °F temperature scale
12.1” (30 cm) color flat panel touch screen display
Resolution: 0.1°C, 0.1%RH, 0.01 for other linear applications
Real time clock included
Sample Rate: Process variable sampled every 0.1 seconds
Proportional Band: Programmable 1.0° to 300°
Control Method: Digital
Intervals: Unlimited
Interval Resolution: 1 sec to 99 hrs,59 min with 1 second resolution
- RS-232
- 10+ Years Data Storage
- Product Temperature Control
- Event Relay Board
Operating Modes: Automatic or Manual
Program Storage: Unlimited
Program Loops:
- Up to 64 loops per program
Loops can be repeated up to 9,999 times program
- Up to 64 nested loops are allowed per
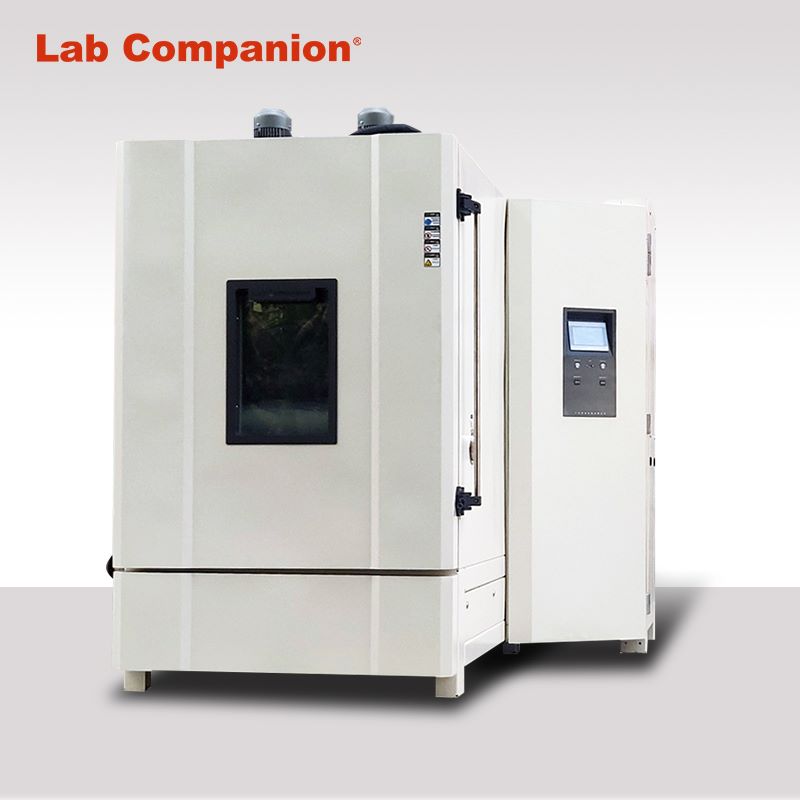