Electric Vehicle Component Reliability Test Solution
In the trend of global warming and gradual consumption of resources, automotive gasoline is also sharply reduced, electric vehicles are driven by electric energy, reducing the heat of internal combustion engine, carbon dioxide and exhaust gas emissions, for energy saving and carbon reduction and improve the greenhouse effect plays a huge role, electric vehicles are the future trend of road transportation; In recent years, the world's advanced countries actively develop electric vehicles, for thousands of components composed of complex products, its reliability is particularly important, a variety of harsh environments are testing the electronic system of electric vehicles [battery cell, battery system, battery module, electric vehicle motor, electric vehicle controller, battery module and charger...], Hongzhan Technology for you to sort out electric vehicle related parts reliability test solutions, hope to be able to provide customers with reference.
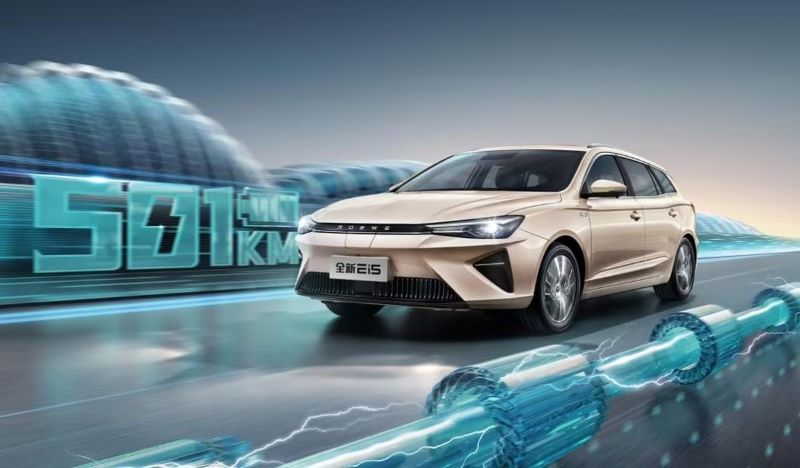
First, different environmental conditions will have different effects on parts and cause them to fail, so the parts of the car need to be tested according to the relevant specifications to meet international requirements and meet the foreign market, the following is the correlation between different environmental conditions and product failure:
A. High temperature will make the product aging, gasification, cracking, softening, melting, expansion and evaporation, resulting in poor insulation, mechanical failure, mechanical stress increase; Low temperature will make the product embrittlement, icing, shrinkage and solidification, mechanical strength reduction, resulting in poor insulation, cracking mechanical failure, sealing failure;
B. High relative humidity will make the product poor insulation, cracking mechanical failure, sealing failure and resulting in poor insulation; Low relative humidity will dehydrate, embrittlement, reduce mechanical strength and lead to cracking and mechanical failure;
C. Low air pressure will cause product expansion, electrical insulation deterioration of the air to produce corona and ozone, low cooling effect and lead to mechanical failure, sealing failure, overheating;
D. Corrosive air will cause product corrosion, electrolysis, surface degradation, increased conductivity, increased contact resistance, resulting in increased wear electrical failure, mechanical failure;
E. Rapid temperature changes will cause local overheating of the product, resulting in cracking deformation and mechanical failure;
F. Accelerated vibration damage or impact will cause the mechanical stress fatigue resonance of the product and lead to an increase in structural damage.
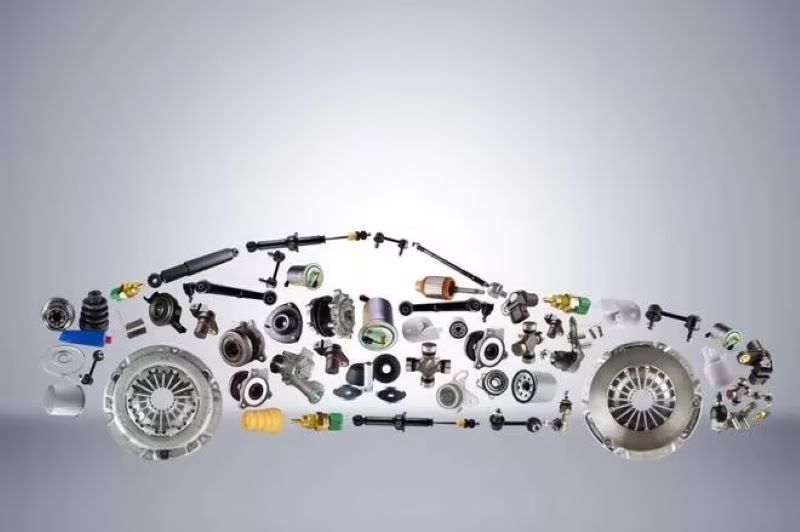
Therefore, products need to pass the following climatic tests to test the reliability of components: Dust (dust) test, high temperature test, temperature and humidity storage test, salt/dry/warm recovery test, temperature and humidity cycle test, immersion/seepage test, salt spray test, low temperature test, thermal shock test, hot air aging test, weather and light resistance test, gas corrosion test, fire resistance test, mud and water test, dew condensation test, high variable temperature cycle test, Rain (waterproof) test, etc.
The following are the test conditions for automotive electronics:
A. IC and interior lights for locomotives,
Recommended model: vibration of the comprehensive chamber
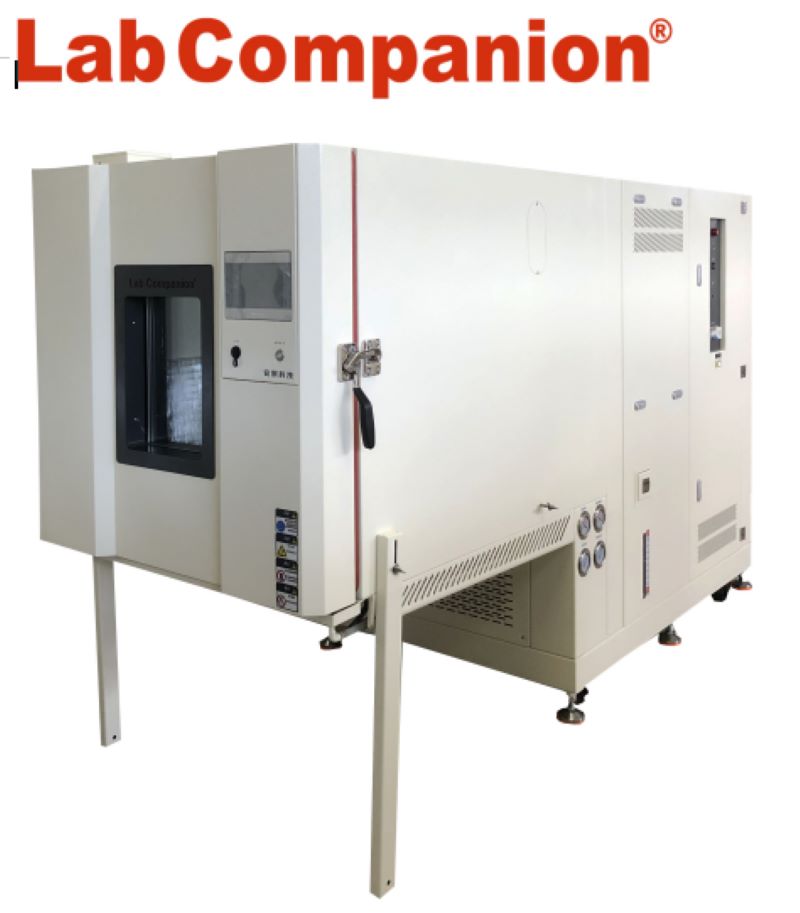
B. Instrument panel, motor controller, Bluetooth headset, tire pressure sensor, GPS satellite positioning system, instrument backlight, interior light, exterior light, automotive lithium battery, pressure sensor, motor and controller, automotive DVR, cable, synthetic resin
Recommended model: constant temperature and humidity test chamber
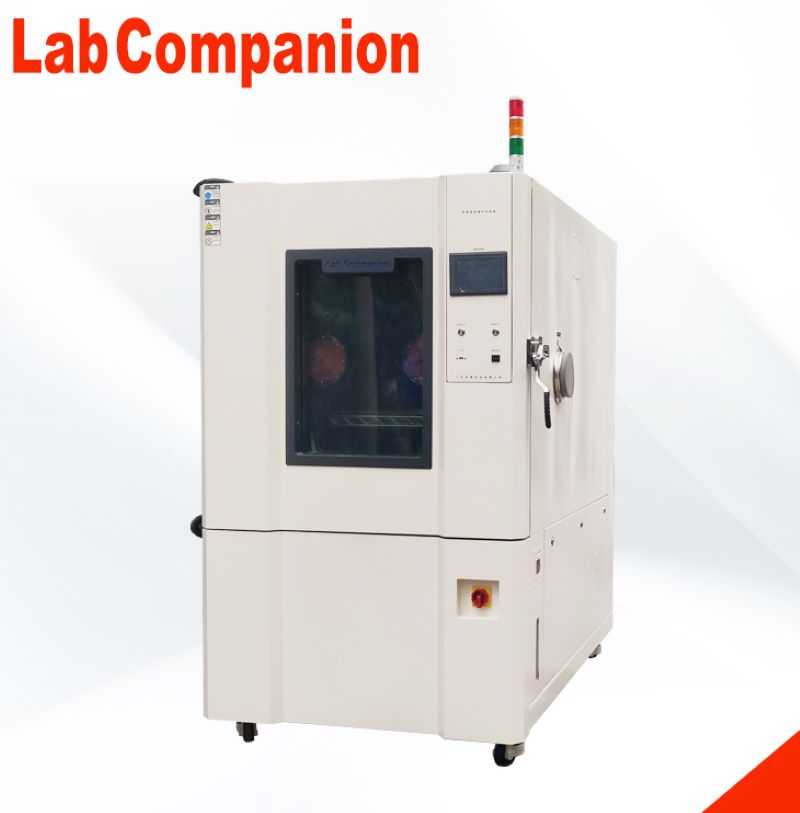
C. 8.4 "LCD screen for cars
Recommended model: thermal stress recombination machine
Second, automotive electronic parts are divided into three categories, including IC, discrete semiconductor, passive components three categories, in order to ensure that these automotive electronic components meet the highest standards of automotive safety. The Automotive Electronics Council(AEC) is a set of standards AEC-Q100 designed for active parts (microcontrollers and integrated circuits...)and AEC-Q200 designed for passive components, which specifies the product quality and reliability that must be achieved for passive parts. AEC-Q100 is the vehicle reliability test standard formulated by the AEC organization, which is an important entry for 3C and IC manufacturers into the international auto factory module, and also an important technology to improve the reliability quality of Taiwan IC. In addition, the international auto factory has passed the safety standard (ISO-26262). AEC-Q100 is the basic requirement to pass this standard.
1. List of automotive electronic parts for A.EC-Q100: Automotive disposable memory, Power Supply step-down regulator, Automotive photocoupler, three-axis accelerometer sensor, video jiema device, rectifier, ambient light sensor, non-volatile ferroelectric memory, power management IC, embedded flash memory, DC/DC regulator, Vehicle gauge network communication device, LCD driver IC, Single power Supply differential Amplifier, Capacitive proximity switch Off, high brightness LED driver, Asynchronous switcher, 600V IC, GPS IC, ADAS Driver Assistance System Chip, GNSS Receiver, GNSS front-end amplifier...
B. Temperature and humidity test conditions: temperature cycle, power temperature cycle, high temperature storage life, high temperature working life, early life failure rate;
2. List of automotive electronic parts for A.AC-Q200: automotive grade electronic components (compliant with AEC-Q200), commercial electronic components, power transmission components, control components, comfort components, communication components, audio components.
B. Test conditions: high temperature storage, high temperature working life, temperature cycle, temperature shock, humidity resistance.