1.Automatic Collar Attaching Machine —The Exquisite Shaping Of Collars
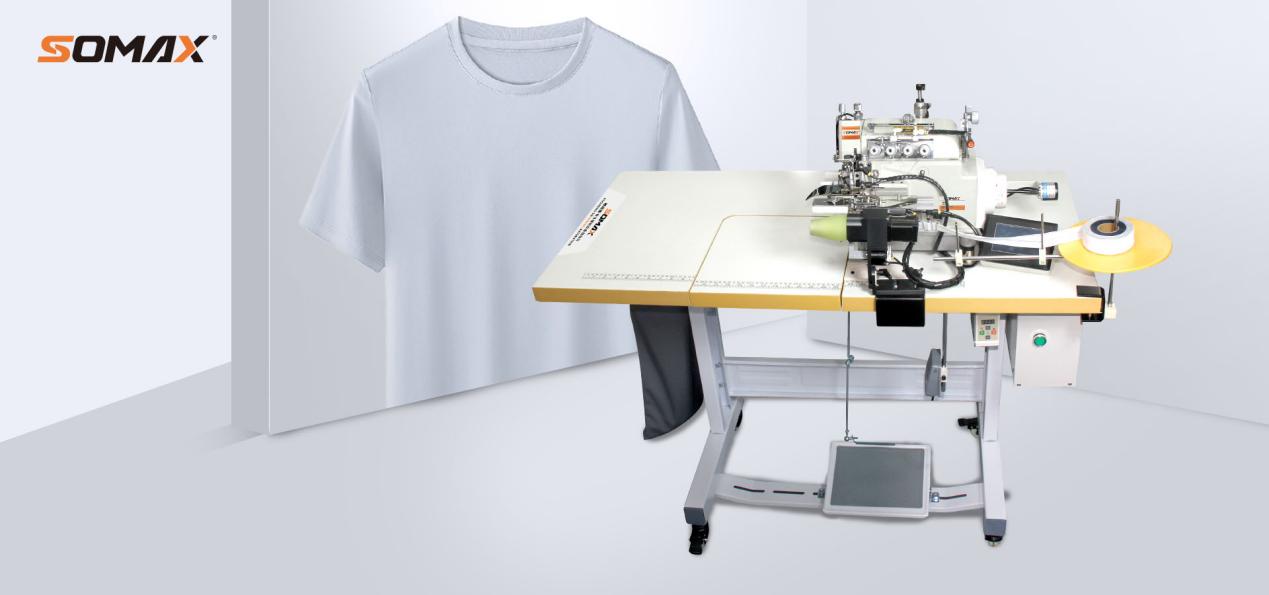
A.Convenient and Efficient Operation
Automatic collar attaching machine is a vanguard in the T-shirt sewing production line, infusing convenience and vitality into the collar-making process. Traditionally, workers had to precisely handle the fit of the collar strip with the neckline fabric, making repeated adjustments and meticulous stitching. Any slight error could result in wrinkles, asymmetry, and other defects, and the output was limited, with a skilled worker managing to complete only dozens of pieces per hour. Now, the automatic collar attaching machine has rewritten this scenario with intelligent control. Workers only need to place the prepared collar strips and garment pieces in order, and the machine can execute precisely according to the preset program.Taking the SOMAX SM-01 series as an example, it can automatically complete collar strip positioning, collar strip layering positioning, and fabric edge positioning. Workers can easily press the foot pedal, and the machine will operate at high speed. Newcomers, after a brief training, can achieve an hourly output of over a hundred pieces, and the efficiency is astonishing when operated by skilled workers. It's like injecting a "powerful stimulant" into production, allowing companies to seize the initiative in the fast-paced market competition.
B.Multi-functional Applications
This machine is not just a one-trick pony for sewing T-shirt round collars; it is also a versatile player in the sewing of garment components. It excels in the fields of sportswear and casual wear, flexibly switching modes to evenly sew elastic waistbands, ensuring a tight fit and comfortable stretch between the elastic band and the fabric. When creating ribbed products with circular waist openings, it can precisely control the stitching and tension, resulting in clear, elastic rib textures that perfectly match the needs of various styles of clothing. Truly achieving "one machine for multiple uses," it greatly expands the boundaries of enterprise production, reduces equipment cost investment, and empowers the layout of diversified products.
2.Computerized Pattern Sewing Machine — Customization Of Patterns At WillI
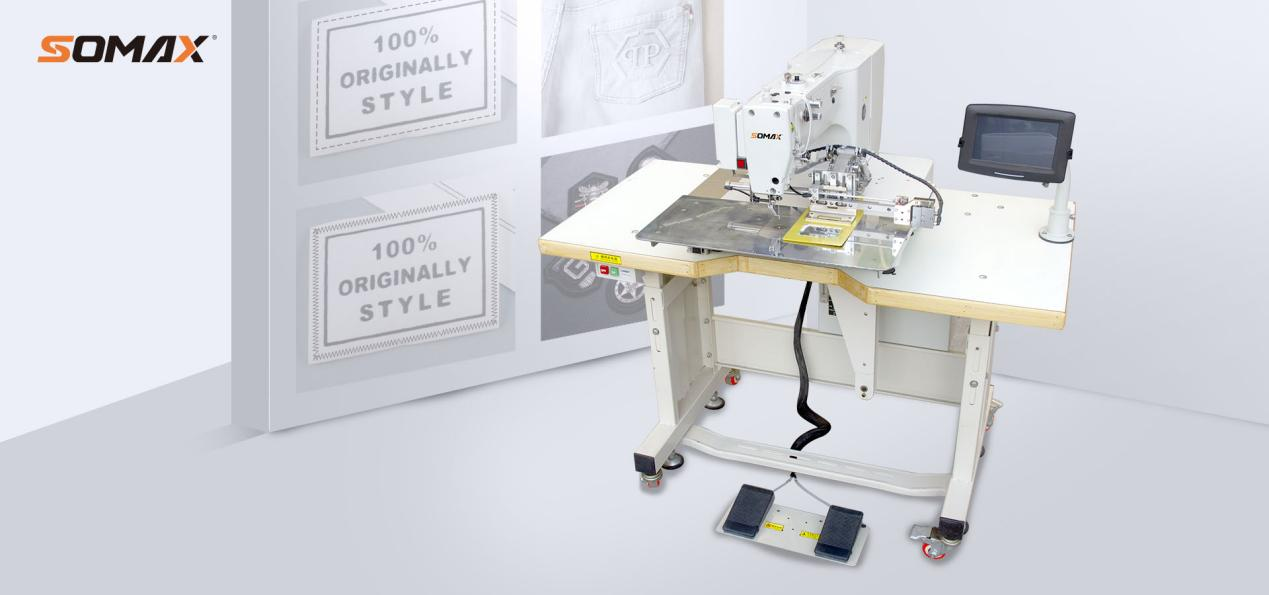
A.Pattern Editing and Storage Function
The computerized pattern sewing machine is like an infinitely creative master tailor, infusing the T-shirt sewing process with a dynamic design soul through its powerful pattern editing and storage capabilities. Within its intelligent electronic control system, operators can easily outline various complex patterns as if drawing an artwork, either through the accompanying software or directly on the machine's touch screen. Whether it's fresh and simple geometric lines, playful and cute cartoon characters, or custom letters and logos that highlight brand personality, they can all be accurately entered and transformed into sewing instructions recognizable by the machine. These patterns are stored in a large-capacity memory, ready for use at any time. Enterprises can, based on different series of T-shirt design requirements, fashion trends, or custom orders from customers, retrieve patterns with one click and quickly switch production. This greatly satisfies the current consumers' pursuit of personalized and fashionable clothing with diverse tastes, allowing each T-shirt to carry a unique charm and empowering brand innovation.
B.Automated Operation Experience
Stepping into the realm of operating a computerized pattern sewing machine, you'll marvel at the convenience and user-friendliness of its automated processes. Operators only need to complete a few steps: input the pattern (either select from a preset library or edit on the spot), place the cut T-shirt fabric flat into the sewing area, lower the press frame to fix the fabric, and lightly press the foot pedal (or simply click the "Start" button on the screen), and the machine will perform the sewing "show" according to the program. Even newcomers to the sewing industry can, after a brief training, quickly master it and produce high-quality patterned sewing products within a few hours.
Moreover, its versatility is extensive, from light and airy chiffon fabrics to thick and durable denim, from soft and skin-friendly cotton to slightly elastic spandex blends, the computerized embroidery machine can accurately adjust to different materials. It shines in various industries such as clothing, bags, footwear, automotive interiors, and more, becoming an indispensable spearhead of modern manufacturing automation.
3.Automatic Bottom Hemming Machine — The Perfect Hemming Of The Bottom Edge
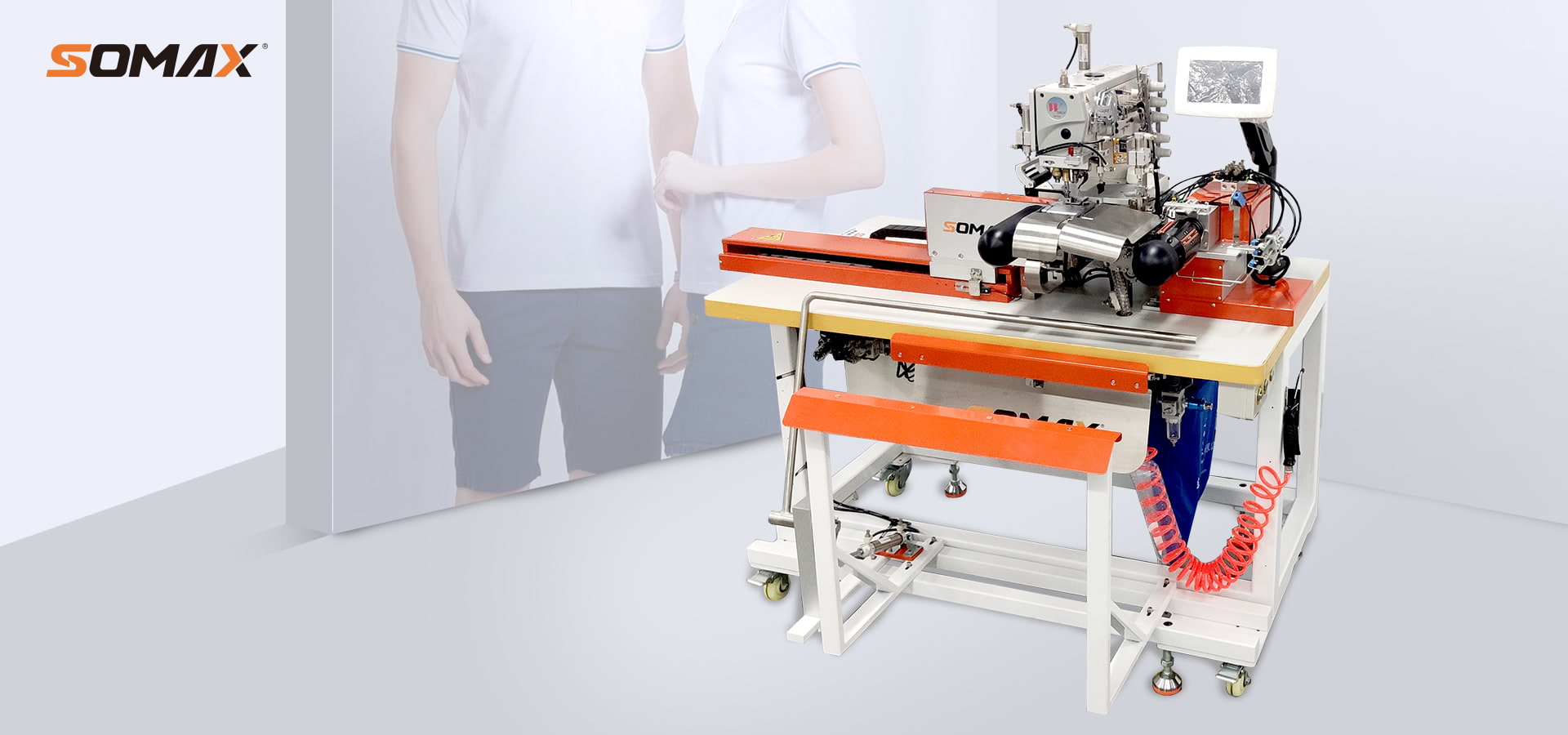
A.Simplified Automated Operation
The automatic bottom hemming machine is like a steady "finishing craftsman," dedicated to giving T-shirts an exquisite finishing touch at the bottom edge. Its introduction simplifies the originally complex hemming process, greatly reducing the demands on manual skills. Operators only need to slip the tubular fabric onto a specific holder, and the machine's built-in intelligent system automatically takes over the subsequent tasks, from precisely stretching the fabric, evenly rolling the edge, to densely sewing, all in one go, without the need for manual adjustments throughout the process. Its operation interface is thoughtfully designed, with a visual display screen that shows real-time equipment status and parameter information. Workers can easily complete fabric loading/unloading and mode switching based on clear instructions, allowing newcomers to quickly get up to speed and seamlessly integrate into the efficient production rhythm, helping enterprises solve the dual challenges of labor training and capacity enhancement.
B.High-Capacity and High-Quality Assurance
In the "examination room" of capacity and quality, the automatic bottom hemming machine performs well. Taking common fabrics such as pure cotton and cotton-polyester blends as examples, it consistently maintains good finished products with even stitching, tight hems, and neat and crisp finished edges, laying a solid foundation for the quality of T-shirts. When faced with order style changes and size variations, it can also adapt flexibly, with convenient electronic control adjustments or modular component replacements, allowing for adaptation adjustments to be completed within just a few minutes, seamlessly connecting to new tasks. This provides a solid backing for enterprises to expand markets and win reputations.
C.Precision Sewing Technology
Diving deep into the core of its craftsmanship, the precision sewing of the automatic bottom hemming machine is truly admirable. Equipped with an advanced automatic size control system, it follows preset parameters such as the width of the hem and stitch spacing. Sensors monitor the fabric feeding and hem rolling dynamics in real-time, precisely controlling the material holding and fabric delivery mechanisms to ensure that every stitch lands exactly as intended. The specially designed material gripping and hem rolling components work in close collaboration to evenly fold the fabric edges, complemented by the sewing head's precise needle bar and shuttle mechanism. As the thread swiftly weaves in and out, the start and end stitches are perfectly aligned, eliminating any deviation. Such fine craftsmanship ensures that the hem of the T-shirt remains smooth and attractive, without curling or deformation, even after numerous washes and wears. It highlights quality through details, enhances brand value, and helps clothing stand out in market competition.
4.Twin Head Automatic Scalding Machine — Precision Branding Of The LOGO
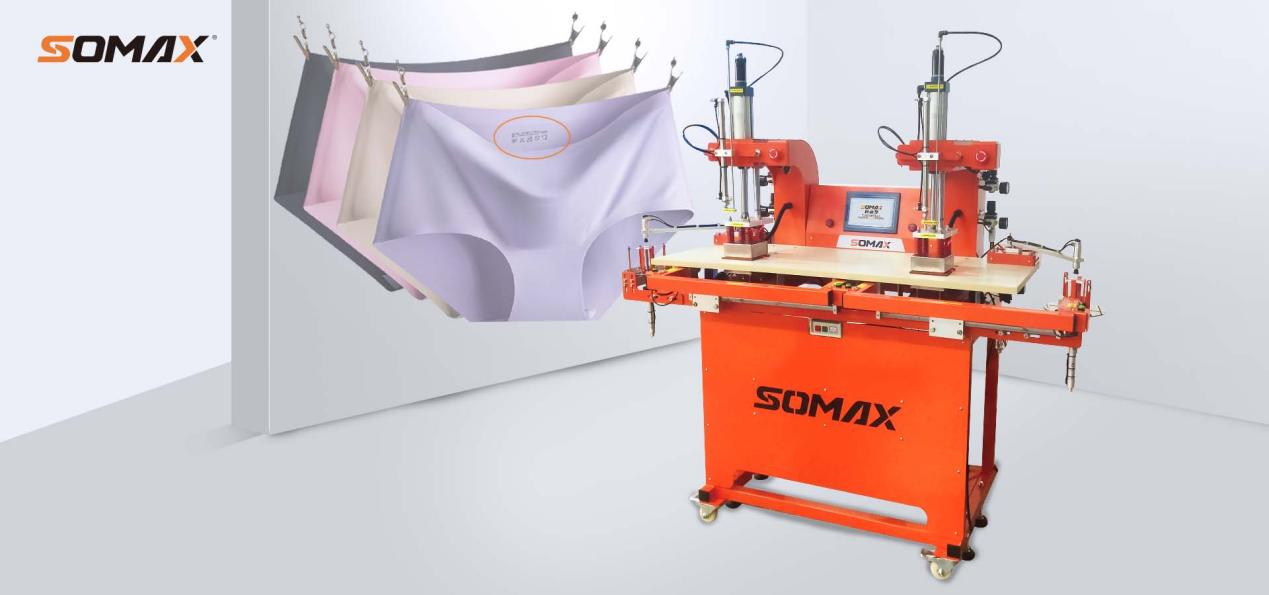
A.Electrical Self-Control Precision Positioning
Twin head automatic scalding machine, as the "branding master" for T-shirt brand logos, rewrites the traditional branding landscape with electrical self-control technology. In the past, manual branding required workers to place the trademark by eye and experience, and press it with an iron, which often resulted in positional deviations of several millimeters, and uneven heating could cause the trademark to wrinkle or peel off, leading to low efficiency and inconsistent quality. Now, with the advent of the branding machine, equipped with a precise electrical control system, taking a SOMAX fully automatic branding machine as an example, its positioning accuracy is up to ±0.2mm. The branding head can follow a preset path and apply the trademark to the designated area with just the right temperature and pressure in a matter of seconds, significantly improving production efficiency by 2-3 times compared to manual methods, and providing a solid quality assurance for brand image output.
B.Multi-functional Design
Multi-functional integration is the "secret weapon" of the scalding machine to meet diverse production needs. It often comes with a multi-station design that integrates material feeding, trademark picking, pressing, and material collection, all in an orderly manner.The vacuum suction cups or mechanical grippers in the trademark picking area quickly grab the trademarks according to instructions, and in coordination with multi-axis robotic arms, they can place the trademarks at various angles. The heating plate in the pressing area is made of high-quality heat conductive materials, paired with an independent temperature control module, which can rapidly heat up to a precise temperature range and apply even pressure, ensuring the trademarks are firmly attached.This multi-functional design meets the various needs of enterprises.
C.Convenient Operation Process
Convenient operation makes the scalding machine a "favorite" piece of equipment in the workshop. Before operation, the power is turned on, the device performs a self-check, and the screen lights up; workers input the appropriate branding temperature (usually 120-180°C) and time (3-10 seconds) based on the T-shirt fabric material (cotton, linen, synthetic fibers, etc.) and the trademark material through the touch screen. During operation, workers only need to feed the material, and the device automatically takes the trademark, brands, and collects the material. Newcomers can get started after half an hour of training, reducing labor costs and enhancing the production vitality of the workshop.
In the production journey of T-shirts, Automatic collar attaching machine,computerized pattern sewing machine,automatic bottom hemming machine, and twin head automatic scalding machine each play their distinct roles, reshaping the production process with the power of automation. They reduce labor costs, enhance product precision, and accelerate delivery cycles, allowing enterprises to move forward steadily in the market tide. Looking to the future, as cutting-edge technologies such as artificial intelligence and the Internet of Things become deeply integrated, garment manufacturing will advance towards intelligence and flexibility.