Introduction:
Background:
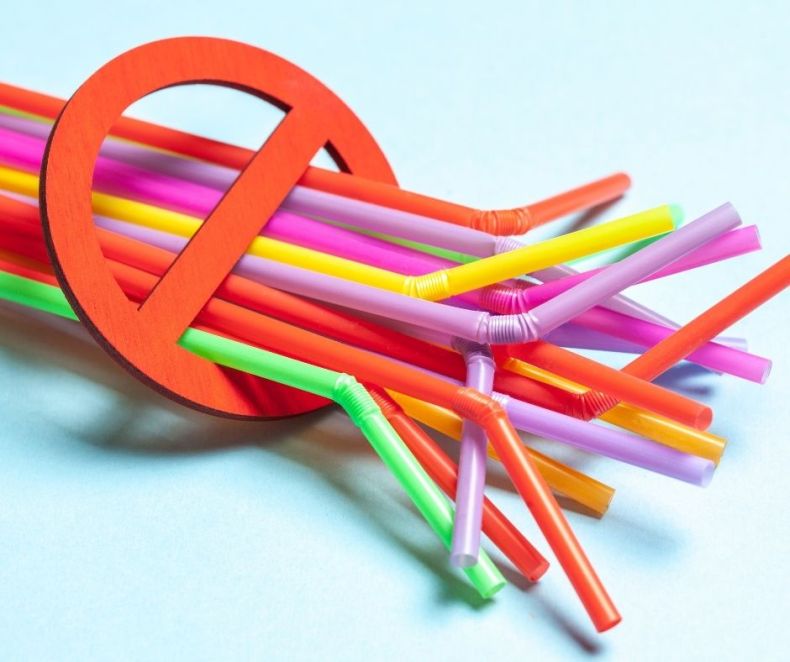
Rise of Biodegradable Straws:
Advantages of PLA Straws:
![]() |
![]() |
Paper Straws Gaining Traction:
Future Development Trends:
Straw Making Machine Technology:
![]() |
![]() |
![]() |
![]() |
![]() |
![]() |
The regular maintenance of straw making machine is very important. we highly suggest our customer to focus on the maintenance .here are several tips for your reference.
The maintenance of the transmission system includes adding and replacing lubricants such as gearbox oil and bearing grease, as well as tensioning the transmission belt.
Gears, sprockets, and chains should be kept clean, and a small amount of calcium-based lubricant should be applied to the gears every half month.
Proper tensioning of the conveyor belt and tightening of the fastening screws for moving parts.
Before starting the machine, check for any foreign objects that may be blocking the machine's interior. Tools of any kind should not be placed on moving parts or above the machine. If any abnormal noises are heard, stop immediately and inspect the machine.
Perform timely inspections and cleaning. After work each day, clean the machine and its surroundings promptly to maintain cleanliness and prevent contamination of the straw.
The following safety considerations should be taken into account when operating a straw making machine/straw packing machine:
Machine maintenance must be performed with the power cut off and the machine completely stopped to ensure safety. Regular maintenance inspections should be carried out, including checks on power supply, lubrication, and wear.
When the machine is in operation, it is strictly forbidden to place fingers near or into moving parts. The straw machine ensures that employees do not leave their posts during operation to avoid emergency situations.
When the machine is in operation, it is strictly forbidden to remove protective covers. The straw machine should be operated with care to avoid unnecessary damage.
The user's power supply should be equipped with overvoltage protection to ensure electrical safety.
The equipment must be reliably grounded.
Strictly follow the instructions on safety signs. Safety signs must be kept clean and should not be covered or removed.
When it comes to the world of paper cup production, selecting the right paper cup making machine is paramount to the success of your business. The choice you make can significantly impact your production efficiency, product quality, and overall profitability. In this comprehensive guide, we will delve into the importance of choosing the right paper cup making machine and provide you with a detailed roadmap to make an informed decision. From considering factors such as production capacity, machine size, cost, and quality, to understanding the different types of machines available and evaluating additional features and customization options, this article will equip you with the knowledge needed to navigate the world of paper cup making machines.
Understanding the Importance of Choosing the Right Paper Cup Making Machine
Choosing the right paper cup making machine is more than just a mere equipment selection. It is an investment that directly influences the success and growth of your business. A well-chosen machine can streamline your production process, enhance efficiency, ensure consistent quality output, and ultimately contribute to your bottom line. On the other hand, selecting the wrong machine can result in inefficiencies, increased costs, and subpar product quality. Therefore, understanding the importance of making an informed decision becomes imperative.
find out which types of paper cup going to produce is most important,like for paper coffee cups, there are single wall,double wall,ripple wall, triple wall, etc
![]() |
as well as the cup sizes, like most common sizes are
The production capacity and speed of a paper cup making machine are crucial factors to consider. The machine's ability to meet the demand for paper cups is directly related to its production capacity. Some machines are designed to produce a high volume of cups in a short span, making them suitable for businesses with large-scale operations and high production requirements. It is essential to evaluate your production needs and match them with the capabilities of the machine to ensure smooth operations.
Low speed like 50-60pcs/min, 65-85pcs/min,medium speed like 80-110pcs.min and high speed around 130-150pcs/min,
in the meantime, your target daily production capacity or weekly production capacity, monthly production capacity must be take into consideration.
The size of the machine and the space it requires in your facility should be carefully evaluated. Different machines have varying dimensions and space requirements. It is crucial to assess the available space in your production area and choose a machine that fits comfortably without hindering other operations. Considering the machine's dimensions and space requirements will help you optimize your workspace and maintain a seamless workflow.
![]() |
Cost and budget considerations play a significant role in the decision-making process. Paper cup making machines are available in a wide price range, depending on their features, capabilities, and automation levels.it start from 10000usd to 50000usd or higher,varies from different types.
While it may be tempting to opt for a machine with the lowest upfront cost, it is crucial to analyze the long-term cost-efficiency and return on investment. Consider factors such as maintenance costs, energy consumption, and potential productivity gains when evaluating the machine's overall cost.
![]() |
The quality and durability of the paper cup making machine are paramount.
Investing in a machine of superior quality ensures reliability, longevity, and consistent performance. Look for machines manufactured by reputable companies known for their expertise in the industry. Conduct thorough research, read customer reviews, and consider the machine's warranty and after-sales support. A durable machine not only minimizes downtime but also ensures the production of high-quality paper cups, contributing to customer satisfaction and retention.
![]() |
Paper cup making machines can be broadly categorized into three types: manual machines, semi-automatic machines, and fully automatic machines. Each type offers unique features and benefits, catering to different production needs and budgets.
Manual machines are entry-level options that require manual intervention at every stage of the cup-making process. Operators perform tasks such as feeding the paper, sealing the cups, and ejecting them manually. These machines are cost-effective but labor-intensive, making them suitable for small-scale operations or businesses with limited budgets.
Semi-automatic machines combine manual and automatic processes, offering a balance between cost and efficiency. These machines automate certain stages of the cup-making process while requiring manual intervention for other tasks. Operators load the paper, and the machine takes care of processes like heating, shaping, and sealing. Semi-automatic machines are ideal for medium-sized operations seeking increased productivity and reduced labor requirements.
Fully automatic machines are the pinnacle of paper cup making technology. They require minimal manual intervention, automating the entire cup-making process from start to finish. These machines offer high-speed production, exceptional efficiency, and precision. They are suitable for large-scale manufacturing operations with high production demands and the need for maximum productivity.
![]() |
Each type of paper cup making machine has its own advantages and disadvantages. Understanding the pros and cons can help you determine which type best aligns with your specific requirements.
Manual machines offer affordability but are time-consuming and labor-intensive. Semi-automatic machines strike a balance between cost and efficiency, providing increased automation while still requiring some manual intervention. Fully automatic machines excel in speed, efficiency, and productivity but come at a higher cost. Evaluating your budget, production needs, and available labor resources will help you identify the most suitable type of machine for your business.
In addition to the basic functionalities, it is essential to consider the availability of additional features and customization options. These can enhance the versatility and capabilities of your paper cup making machine. Some machines offer features such as adjustable cup sizes, color printing capabilities, embossing options, and the ability to accommodate various types of materials. Customization options allow you to cater to specific customer demands and differentiate your products in the market. Carefully assess these features and customization options to ensure they align with your business goals and target market.
Maintaining your paper cup making machine in optimal condition is crucial for uninterrupted production and longevity. Follow the manufacturer's recommended maintenance practices and establish a regular maintenance schedule. This includes routine inspections, lubrication, cleaning, and timely replacement of wear parts. Additionally, familiarize yourself with troubleshooting techniques to identify and resolve common issues that may arise during operation. Promptly addressing any malfunctions or abnormalities will minimize downtime and ensure consistent productivity.
Choosing the right paper cup making machine is a critical decision that significantly impacts your business's success. Consider factors such as production capacity, machine size, cost, and quality to make an informed choice. Evaluate the different types of machines available, understanding their pros and cons, and select the one that aligns with your specific requirements. Assess additional features and customization options to enhance your production capabilities and cater to customer preferences. Implement best practices for maintenance and troubleshooting to maximize the machine's efficiency and lifespan.
By carefully considering these factors and following the guidelines presented in this article, you can make a well-informed decision and set your paper cup manufacturing business on the path to success.
We, a leading manufacturer of paper cup machines, straw making machines in china, dedicated to the development and manufacturing of high quality, more affordable machines to the customer around the world. should you have any request for the paper cup machine, please let us know your cup sizes, production capacity,cup types,so we can give a quotation in a short time.
Paper cups are an integral part of our daily lives, especially in the food and beverage industry. From coffee shops and fast food chains to hospitals and event venues, the demand for disposable cups is skyrocketing. With an increasing emphasis on sustainability, paper cups have emerged as a more eco-friendly alternative to plastic. This shift has, in turn, spurred the need for efficient paper cup machines capable of meeting high production demands while adhering to environmental standards. This guide aims to provide a comprehensive overview of paper cup machines, helping you understand their technical specifications, applications, and future trends, so you can make an informed decision when investing in the right machine for your needs.
1.1 Understanding Machine Capacity
When selecting a paper cup machine, one of the first things to consider is its capacity. This refers to the machine's ability to produce a specific number of cups per minute (CPM). High-speed machines can produce anywhere from 60 to 100 cups per minute, making them ideal for large-scale operations. However, if you're running a smaller business or just starting, a machine with a lower CPM may suffice. Another important factor is the cup size range. Some machines are designed to handle a wide range of sizes, from small espresso cups to large soda cups, while others are more specialized. Understanding your specific production needs will help you determine the right capacity for your business. Additionally, it's important to consider power consumption. Machines with higher production rates typically consume more power, so balancing production efficiency with energy costs is crucial for long-term profitability.
1.2 Material Compatibility
The type of paper and coatings used in the production of paper cups can significantly affect the machine's performance. Most paper cup machines are designed to work with specific paper thicknesses, typically ranging from 150 to 400 grams per square meter (GSM). The thickness of the paper influences the rigidity and insulation properties of the cups, which are important considerations depending on the intended use. Coatings are another critical aspect, with Polyethylene (PE) being the most common for waterproofing and heat resistance. However, with growing environmental concerns, there's a shift towards biodegradable coatings like Polylactic Acid (PLA). It's essential to choose a machine that is compatible with the types of materials you plan to use. Additionally, if you require printed cups, consider the types of inks the machine can work with. Water-based inks are a popular eco-friendly option, but you must ensure your machine can handle these without compromising print quality.
1.3 Machine Dimensions and Weight
The physical dimensions and weight of a paper cup machine are important considerations, especially when space is limited. Most industrial paper cup machines are relatively large, requiring significant floor space. It's important to ensure that the machine's footprint fits comfortably within your production area, with enough room for operators to work safely and efficiently. Weight is another factor, particularly for installations where the machine needs to be moved frequently. Heavier machines offer more stability but can be challenging to transport or reposition. If portability is a priority, consider machines designed for easier movement, although this might come at the expense of production capacity or speed. When planning your setup, account for additional space for materials, maintenance access, and storage.
1.4 Automation Level
The level of automation in paper cup machines varies widely, from manual models that require constant operator intervention to fully automated systems that can run with minimal supervision. Manual machines are generally more affordable and are suitable for small-scale operations or businesses with tight budgets. However, they require more labor and can be less consistent in output. On the other hand, fully automated machines, while more expensive, offer significant advantages in terms of speed, consistency, and labor savings. They typically come with advanced control systems that allow for easy monitoring and adjustment of production parameters. Semi-automatic machines offer a compromise, providing some level of automation while still requiring human oversight. Understanding the level of automation that best suits your production needs is essential for maximizing efficiency and return on investment.
1.5 Maintenance Requirements
Regular maintenance is crucial to keep paper cup machines running smoothly and to avoid costly downtime. Each machine comes with its own set of maintenance requirements, ranging from daily cleaning tasks to periodic replacement of wear parts. Routine maintenance tasks typically include cleaning the paper feed system, lubricating moving parts, and inspecting for wear and tear. The availability of spare parts is another important consideration; machines from well-known manufacturers often have better support networks, making it easier to source replacement parts. Maintenance costs can add up over time, so it's important to factor these into your overall operating expenses. Some manufacturers offer maintenance contracts, which can provide peace of mind and potentially lower long-term costs by ensuring regular professional upkeep.
![]() |
2.1 Food and Beverage Industry
The food and beverage industry is the primary market for paper cup machines. Restaurants, cafes, and coffee shops rely heavily on disposable cups for serving beverages like coffee, tea, and soft drinks. Paper cups offer a convenient and hygienic way to serve drinks on the go, and with the growing trend of custom branding, many businesses are opting for machines that can produce cups with personalized prints and logos. For event catering, the ability to produce large quantities of cups in a short time is essential. Events like festivals, concerts, and conferences require vast numbers of disposable cups, making high-capacity paper cup machines indispensable. Additionally, the integration of paper cups with vending machines has seen a rise in demand for specialized machines that can produce cups suitable for hot beverages, ensuring they maintain their structure and do not leak or degrade when filled with hot liquids.
2.2 Healthcare and Hospitals
In healthcare settings, paper cups are used extensively due to their disposable nature, which helps maintain hygiene and prevent cross-contamination. Hospitals and clinics often use paper cups for dispensing medications, serving water to patients, and in laboratories for sample collection. The demand for sterile, high-quality cups has led to the development of machines that can produce cups meeting the strict standards required in medical environments. These specialty cups often need to be produced in controlled environments to ensure they are free from contaminants. As such, machines used in healthcare settings are typically designed with additional features to ensure compliance with health regulations, such as automated cleaning systems and the use of sterile materials.
2.3 Retail and Wholesale Distribution
The retail sector also plays a significant role in the demand for paper cup machines. Many retail brands, particularly those in the food and beverage sector, opt for private labeling to differentiate their products. This has led to an increase in the demand for paper cup machines capable of producing custom-branded cups in bulk. Wholesale distributors also rely on high-capacity machines to meet the demands of large orders. For businesses involved in retail and distribution, the ability to produce a variety of cup sizes and designs is crucial, as it allows them to cater to different market segments. Moreover, the rise of e-commerce has opened up new opportunities for retail brands to offer personalized products, further driving the need for versatile paper cup machines.
2.4 Environmental Applications
As the world becomes more conscious of environmental issues, the demand for eco-friendly paper cups has increased. Paper cup machines that produce biodegradable or compostable cups are now at the forefront of the industry. These machines are designed to work with environmentally friendly materials such as PLA coatings, which are derived from renewable resources like corn starch and are fully compostable. In addition to producing cups, some machines are integrated with recycling programs, allowing businesses to recycle used cups and reduce waste. This not only helps companies meet their sustainability goals but also appeals to environmentally conscious consumers who prefer brands that prioritize eco-friendly practices. The environmental applications of paper cup machines are not just a trend but a growing necessity in an industry moving towards a more sustainable future.
3.1 Environmental Impact
One of the most significant benefits of paper cup machines is their positive impact on the environment compared to plastic alternatives. Paper cups, especially those made from recycled or sustainably sourced paper, decompose much faster than plastic cups, reducing the burden on landfills. The shift towards biodegradable and compostable paper cups further enhances this environmental benefit. By using paper cup machines, businesses can contribute to reducing plastic waste, which is a major concern globally. Moreover, producing paper cups locally using these machines can reduce the carbon footprint associated with transporting cups from manufacturers to end-users. Sustainability certifications, such as those from the Forest Stewardship Council (FSC), further validate the environmental credentials of paper cup production, making it easier for companies to demonstrate their commitment to sustainability.
3.2 Cost Efficiency
In addition to environmental benefits, paper cup machines offer significant cost advantages. While the initial investment in a machine can be substantial, the long-term savings in production costs are considerable. Producing cups in-house eliminates the need to purchase pre-made cups, which can be more expensive, especially when factoring in shipping costs. Energy-efficient machines further contribute to cost savings by reducing electricity consumption. The automation provided by modern paper cup machines also leads to labor savings, as fewer operators are needed to run the machine compared to manual production methods. Additionally, by producing cups on-demand, businesses can better manage their inventory, reducing waste and the costs associated with storing large quantities of pre-made cups.
3.3 Customization Capabilities
Another major benefit of paper cup machines is their ability to produce customized cups.
Branding is crucial in today's competitive market, and custom-printed paper cups offer a unique opportunity for businesses to reinforce their brand identity. With the right machine, companies can produce cups with their logos, slogans, and even seasonal designs, helping to create a memorable customer experience. The flexibility to switch between different cup sizes and designs also allows businesses to cater to a broader range of customer preferences. Customized cups can also enhance consumer perception, as they are often associated with higher quality and professionalism. For businesses looking to differentiate themselves in a crowded market, the ability to produce branded paper cups in-house is a valuable asset.
4.1 Advanced Automation Technologies
The latest paper cup machines are increasingly incorporating advanced automation technologies to improve efficiency and reduce waste. One of the most significant advancements is the integration of artificial intelligence (AI), which allows machines to optimize production processes in real-time. AI can help reduce material waste by adjusting settings based on the quality of the input materials, ensuring consistent output without human intervention. Smart sensors are another innovation that enhances machine efficiency by monitoring various parameters, such as temperature and pressure, and making adjustments as needed. These sensors can also detect potential issues before they lead to breakdowns, reducing downtime and maintenance costs. Remote monitoring systems are becoming more common, allowing operators to track machine performance and make adjustments from anywhere with an internet connection. This not only improves efficiency but also provides greater flexibility in managing production.
4.2 New Material Technologies
Innovations in material technologies are also driving changes in the paper cup industry. One of the most promising developments is the use of bio-based coatings, such as PLA, which offer a more sustainable alternative to traditional PE coatings. PLA is made from renewable resources and is fully compostable, making it an attractive option for environmentally conscious consumers. Additionally, there has been a growing interest in using recycled paper for cup production, which further reduces the environmental impact. New ink and printing technologies are also being developed to work with these sustainable materials. For example, water-based inks, which are less harmful to the environment, are becoming more widely used. These innovations not only enhance the sustainability of paper cups but also open up new opportunities for businesses to differentiate themselves by offering eco-friendly products.
4.3 Energy-Efficient Models
As energy costs continue to rise, the demand for energy-efficient paper cup machines has grown. Manufacturers are responding by developing models that consume less power without compromising on performance. Some of these machines are designed with low-power consumption motors and energy-efficient heating systems that reduce the overall energy usage during production. Solar-powered paper cup machines are another exciting innovation, offering a way to produce cups with minimal environmental impact. These machines use solar panels to generate the electricity needed for production, making them an ideal choice for businesses looking to reduce their carbon footprint. Additionally, some machines are equipped with heat recovery systems that capture and reuse the heat generated during production, further enhancing energy efficiency and reducing operational costs.
5.1 Market Trends and Growth Projections
The global demand for paper cups is expected to continue growing, driven by increasing environmental awareness and government regulations aimed at reducing plastic waste. As more consumers shift towards eco-friendly products, the market for paper cup machines is also expected to expand. Growth is particularly strong in regions with stringent environmental regulations, such as Europe and North America, where businesses are increasingly required to use sustainable packaging. Emerging markets in Asia and Africa are also seeing significant growth, driven by rising incomes and the expansion of the food and beverage industry. Consumer behavior is another key driver, with more people willing to pay a premium for sustainable products. This trend is expected to continue, with projections indicating steady growth in demand for paper cups and the machines that produce them.
5.2 Regulatory Changes and Impacts
Government regulations play a crucial role in shaping the paper cup industry. In many regions, regulations are becoming stricter, with bans on single-use plastics and mandates for sustainable packaging. These changes are driving innovation in the paper cup machine industry, as manufacturers develop new technologies and materials to meet regulatory requirements. For example, the European Union's Single-Use Plastics Directive has led to a surge in demand for biodegradable and compostable paper cups. In response, manufacturers are focusing on developing machines that can produce cups meeting these new standards. Sustainability standards, such as those from the FSC and the Programme for the Endorsement of Forest Certification (PEFC), are also influencing machine design and operation, as businesses seek to comply with these certifications. As regulations continue to evolve, staying ahead of these changes will be crucial for businesses in the paper cup industry.
5.3 Innovations on the Horizon
Looking to the future, several exciting innovations are on the horizon for the paper cup industry. One of the most promising is the potential for 3D printing in paper cup production. This technology could revolutionize the industry by allowing for highly customized designs and reducing material waste. Nanotechnology is another area of interest, with the potential to create more durable and heat-resistant coatings for paper cups. This could lead to the development of cups that are even more environmentally friendly while maintaining the necessary functionality for hot beverages. The move towards a circular economy is also expected to drive innovation, with more emphasis on recycling and reusing materials. Future paper cup machines may be designed with these principles in mind, allowing for the production of cups that are not only sustainable but also fully integrated into a closed-loop system.
![]() |
6.1 Paper Cups vs. Plastic Cups
When comparing paper cups to plastic cups, the most significant difference lies in their environmental impact. Plastic cups are notorious for their contribution to global plastic pollution, taking hundreds of years to decompose. In contrast, paper cups, especially those made from recycled or sustainably sourced paper, decompose much faster, reducing their impact on landfills. However, it's important to note that not all paper cups are created equal. Those with plastic coatings can be more challenging to recycle, although they still represent a better option than fully plastic cups. In terms of cost, plastic cups are often cheaper to produce, but this advantage is diminishing as environmental regulations and consumer preferences shift towards more sustainable options. Additionally, consumer perceptions play a significant role in this comparison, with many people now viewing paper cups as the more responsible choice.
6.2 Paper Cups vs. Reusable Cups
The debate between single-use paper cups and reusable cups is ongoing, with valid arguments on both sides. Reusable cups, made from materials like stainless steel or glass, offer the obvious advantage of reducing waste. However, they also require energy and resources to produce, and they need to be washed after each use, which consumes water and electricity. For businesses, the choice between offering paper or reusable cups often comes down to the specific context. For example, paper cups may be more practical for events or fast food outlets where convenience and hygiene are top priorities. On the other hand, reusable cups might be a better option for sit-down restaurants or cafes where customers are encouraged to reduce waste. It's also worth considering the lifecycle costs of reusable cups, which can be higher than paper cups when factoring in the costs of cleaning and potential breakage.
6.3 Paper Cups vs. Other Biodegradable Alternatives
In addition to paper cups, several other biodegradable materials are being used to produce disposable cups, including bamboo, corn starch, and sugarcane. These materials offer the advantage of being fully biodegradable and often compostable, making them an attractive option for environmentally conscious consumers. However, they also come with their own set of challenges. For example, bamboo cups can be more expensive to produce, and they may not be as widely accepted in the market as paper cups. Corn starch and sugarcane cups are often used in regions with access to industrial composting facilities, as they require specific conditions to break down effectively. When compared to paper cups, these alternatives can offer similar environmental benefits but may involve higher production costs or limited availability. For businesses looking to adopt biodegradable alternatives, it's important to consider the full lifecycle of the product and the infrastructure available for disposal.
7.1 Setup and Installation
Setting up a paper cup machine requires careful planning and preparation. The first step is to ensure that the production site meets all the necessary requirements, including adequate space, power supply, and ventilation. Most machines will need a dedicated area with stable flooring to support the weight of the equipment. The installation process typically involves positioning the machine, connecting it to the power source, and calibrating the settings according to the manufacturer's instructions. It's essential to follow the installation steps carefully to avoid any issues during operation. Initial calibration is crucial to ensure that the machine is producing cups of the correct size and quality. This may involve adjusting the paper feed, heating elements, and cutting mechanisms. Once the machine is set up and calibrated, it's ready to start production, but it's important to monitor the first few production runs closely to ensure everything is functioning correctly.
7.2 Daily Operation and Workflow
Operating a paper cup machine involves several daily tasks to ensure smooth production. The day typically starts with powering up the machine and checking that all systems are functioning correctly. This includes inspecting the paper feed, checking the ink levels (if printing is involved), and ensuring that the heating elements are at the correct temperature. During production, it's important to monitor the machine continuously, watching for any signs of malfunction or quality issues. This might involve checking the alignment of the paper, the consistency of the prints, and the structural integrity of the cups. Quality control is an ongoing process, with operators regularly inspecting the finished products to ensure they meet the required standards. If any issues are detected, the machine settings may need to be adjusted, or the machine may need to be stopped temporarily to address the problem.
7.3 Troubleshooting Common Issues
Even with the best maintenance practices, paper cup machines can encounter issues that disrupt production. One of the most common problems is machine jams, which can occur if the paper feed is misaligned or if there is a blockage in the cutting mechanism. To clear a jam, the machine must be stopped, and the obstruction carefully removed. It's important to address the root cause of the jam to prevent it from recurring. Ink and printing problems are another common issue, particularly if the machine is not properly calibrated. Poor print quality, misalignment, or smudging can all impact the appearance of the final product. These issues can often be resolved by adjusting the print settings or replacing the ink cartridges. Paper feed errors, such as misfeeds or double feeds, can also occur and may require adjustments to the paper tension or feed rollers. Regular troubleshooting and maintenance are key to minimizing downtime and ensuring consistent production.
7.4 Regular Maintenance and Care
Regular maintenance is essential to keep paper cup machines running efficiently and to extend their lifespan. Daily cleaning is one of the most important maintenance tasks, as it helps prevent contamination and buildup of materials that can affect machine performance. This typically involves cleaning the paper feed, cutting blades, and heating elements. Lubrication is another critical task, as it ensures that all moving parts operate smoothly and reduces wear and tear. Depending on the machine, certain parts may need to be replaced periodically, such as cutting blades, seals, or heating elements. Keeping a maintenance schedule helps ensure that these tasks are performed on time and reduces the risk of unexpected breakdowns. Many manufacturers provide detailed maintenance guides, and following these recommendations can help prevent common issues and keep the machine in optimal condition.
![]() |
Paper cup machines are an essential tool for businesses in the food and beverage, healthcare, and retail industries, offering a sustainable alternative to plastic cups. By understanding the technical specifications, applications, benefits, challenges, and future trends associated with these machines, businesses can make informed decisions that align with their production needs and environmental goals. Whether you're looking to start a new business or expand an existing operation, choosing the right paper cup machine is crucial for success. With the right machine, you can produce high-quality, customized paper cups that meet the demands of your customers while minimizing your environmental impact. As the industry continues to evolve, staying informed about the latest innovations and trends will help you stay competitive and achieve long-term success.
If you have any request for a paper cup machine, please feel free to contact us to get a support.
Welcome to our comprehensive guide, where we unravel the intricacies of U-shaped drinking straw production. In a world that constantly evolves, even the simplest of objects undergo innovative transformations. One such transformation is the humble drinking straw, now taking on the dynamic and functional form of the U-shaped straw.
In this blog, we embark on a journey through the world of U-shaped drinking straws, delving into their creation, applications, and the entire production process. From the initial concept to the final packaged product, we'll unravel each step to thoroughly understand how these straws are manufactured and why they're gaining prominence across various industries.
So, whether you're a curious consumer wanting to know more about the straws you use or an entrepreneur seeking to delve into the world of straw production, this guide has you covered. Join us as we dive deep into the world of U-shaped drinking straw production, exploring its applications, production process, considerations for setting up a production line, and much more. Get ready to become well-versed in all things U-shaped straw-related – the knowledge you need is right here at your fingertips.
![]() |
Imagine a drinking straw that's not just a straight conduit but a cleverly designed tool that adapts to various scenarios – that's the essence of the U-shaped drinking straw. These innovative straws have taken the beverage consumption experience to a new level, offering functionality that goes beyond the conventional.
![]() |
Definition and Characteristics:
A U-shaped drinking straw, as the name suggests, features a distinct U-shape along its length. This design departure from the traditional straight straw offers several advantages. The curvature allows for better reach and accessibility, making it ideal for a wide range of users, including those with mobility constraints or specific medical needs. The straws are typically made from safe and food-grade plastic materials, ensuring a seamless and hygienic drinking experience.
Advantages of U-shaped Design:
The U-shaped design of these straws brings forth a host of benefits. It enables ease of use in situations where tilting the head might be difficult or uncomfortable, such as when lying down or reclining. Additionally, the design is versatile enough to suit both hot and cold beverages, making it a convenient option for a variety of drinks.
Comparison with Traditional Straight Straws:
In contrast to the conventional straight straws, U-shaped drinking straws provide a more user-centric experience. While straight straws may require users to contort their bodies for effective sipping, U-shaped straws adapt to the user's posture, promoting a more natural and comfortable drinking motion. This adaptability also reduces the risk of spills and choking incidents, making them a safer choice, especially for individuals with limited motor control.
Visual Representation:
Visualizing the U-shaped design is crucial to understanding its significance. Picture a straw with a gentle bend in the middle, resembling the letter 'U.' This bend facilitates an ergonomic and functional approach to drinking, catering to a broader audience and a wider range of situations.
The next section of our blog will take us through the exciting realm of applications where U-shaped drinking straws truly shine. From healthcare settings to day-to-day convenience, these straws have found their way into various industries, addressing specific needs and revolutionizing the way we sip our favorite beverages. Join us as we explore the diverse landscapes these straws have conquered.
The innovation of U-shaped drinking straws has brought about a paradigm shift in how we approach beverage consumption. This design, once seen as a simple alteration, has sparked a revolution across multiple industries, each benefiting from the unique advantages these straws offer.
![]() |
1. Healthcare and Medical Settings:
U-shaped drinking straws have found a significant role in healthcare environments. For patients with mobility limitations, such as those bedridden or with reduced motor control, these straws provide a dignified and practical solution. Medical professionals often opt for U-shaped straws to ensure patients can enjoy beverages comfortably without compromising their posture or recovery process.
2. Special Needs and Disabilities:
Individuals with disabilities or special needs often face challenges while consuming liquids. U-shaped drinking straws address these challenges by accommodating different postures and making drinking more accessible. This inclusivity enhances the overall quality of life for those with varying abilities.
3. Hospitality and Food Services:
In the hospitality sector, the guest experience is paramount. U-shaped straws elevate the dining experience, allowing patrons to enjoy their drinks without awkward adjustments. These straws are particularly popular in upscale restaurants, hotels, and catering services where attention to detail matters.
4. Home Use and Convenience:
Beyond specific industries, U-shaped straws have also made their way into homes. Whether it's parents ensuring their young children can comfortably sip from a cup or individuals seeking a more relaxed way to enjoy beverages, these straws cater to everyday convenience.
5. Elderly Care:
As our population ages, the importance of products catering to the elderly becomes more evident. U-shaped straws offer seniors a comfortable and spill-free way to hydrate, promoting independence and maintaining their dignity.
6. Travel and On-the-Go:
For those constantly on the move, U-shaped straws are a travel essential. Whether on a plane, train, or in a car, these straws allow for easy sipping without requiring users to tilt their heads or worry about spills.
7. Sports and Active Lifestyles:
Athletes and fitness enthusiasts often require quick and convenient hydration. U-shaped straws fit into water bottles and hydration packs, ensuring smooth sipping during workouts or outdoor activities.
8. Sustainability Initiatives:
Some manufacturers offer U-shaped straws made from eco-friendly materials, aligning with sustainability goals. This showcases the versatility of these straws in catering to both functional and environmental concerns.
In the subsequent sections of this blog, we'll delve into the intricate production process of U-shaped drinking straws. From the initial straw extrusion to the final packing in cartons, we'll uncover the stages that transform raw materials into these functional and adaptive tools. Join us as we explore the manufacturing journey that gives life to U-shaped drinking straws.
Step-by-step breakdown of the entire production process:
![]() |
|||
![]() |
![]() |
![]() |
![]() |
1. Straw extrusion machine: Making the straight straw | 2. Flexible straw bending machine: Bend the straight straw into flexible | 3. U-shaped straw bending & packing machine: Formation of the U-shape and packaging. | 4. Straw Auto Carton Packing Machine: Final packing in carton, Bulk packaging for distribution. |
Investing in a U-shaped drinking straw production line is a significant decision that requires careful consideration of various factors. To ensure a successful venture into this innovative industry, here are the key aspects you need to evaluate before making your investment:
1. Quality Standards and Certifications:
Ensure that the production line adheres to relevant quality standards and certifications for the industry. These standards guarantee that your U-shaped straws meet safety and hygiene requirements, boosting your credibility among clients and end-users.
2. Production Capacity and Speed:
Determine your required production capacity and speed. then will know how many lines are required.
3. Customization Options:
Consider whether the production line allows for customization of U-shaped straw designs. Depending on your target market, the ability to offer unique designs, colors, and features could give you a competitive edge.
4. Energy Efficiency and Sustainability:
As environmental concerns grow, opt for a production line that integrates energy-efficient practices and sustainable materials. A commitment to eco-friendly production can enhance your brand reputation and appeal to environmentally conscious consumers.
5. Maintenance and Support Services:
Evaluate the availability of maintenance and support services. A reliable supplier should provide training for your staff, technical assistance, and access to spare parts to minimize downtime and keep your production running smoothly.
6. Cost Analysis:
Perform a thorough cost analysis that includes the initial investment, operational costs, maintenance expenses, and potential returns. This analysis will help you gauge the financial viability of your production line.
7. Market Research:
Conduct comprehensive market research to understand the demand for U-shaped drinking straws in your target industries. Identifying potential clients and their requirements will guide your production line choices.
8. Supplier Reputation and Reviews:
Choose a reputable supplier with a track record of delivering high-quality production lines. Look for reviews and testimonials from other clients to gauge their satisfaction and the performance of the equipment.
9. Regulatory Compliance:
Ensure that the production line meets all regulatory requirements and safety standards in your region. This includes aspects such as machine safety, worker safety, and environmental regulations.
10. Technology and Innovation:
Consider the technological features of the production line. Advanced automation and smart technology can improve efficiency and reduce human error in the production process.
By carefully evaluating these factors and making informed decisions, you can set the foundation for a successful U-shaped drinking straw production venture. In the following section, we'll address some of the most common questions that arise when considering such a production line, providing you with insights to guide your decision-making process.
1. What information shall we provide if want to set up a line for u shaped straw making?
--- straw information, like straw material, straw size,straw packing, expected production capacity, your local voltage, etc
2. Can this U shaped straw packing machine works on different sizes straws?
--- it can bend and pack different sizes straw after changing some parts.
3. Is it easy to operate these machines?
--- Workers can operate these machine easily after get trained.
4. Can you give technical support and training support?
--- Yes, absolutely ,we can give technical support at any time. Service is very important
In this guide, we've unveiled the world of U-shaped drinking straws, showcasing their versatility and unique applications. These straws have evolved to offer comfort and convenience, catering to various industries and lifestyles.
Whether it's healthcare, special needs, hospitality, or sustainability, U-shaped straws have made their mark, revolutionizing how we sip beverages. If you're considering entering the U-shaped straw production industry, remember to prioritize quality, capacity, customization, and sustainability.
We invite you to explore the potential of U-shaped straw production, whether as a consumer seeking better sipping or an entrepreneur looking to innovate. The U-shaped straw is here to stay, offering adaptability and enhanced functionality for a wide range of scenarios. Embrace this exciting evolution in drinking straws and join the revolution.
if you need a complete solution for the line, please feel free to contact us.
![]() |
![]() |
![]() |
![]() |
A flexible straw bending machine is a type of machine that is designed to bend straight straws into a specific shape, usually in a U shape. The machine typically consists of several parts like hopper, straw conveyor,control box, forming roller, drum, forming needles,etc.The straight straw are loaded in the hopper, with the forming roller & forming needle, each straight straw will be bended and formed into flexible straw with typically 11teeths or 10teeths.
![]() |
![]() |
![]() |
Flexible straw bending machines are commonly used in the manufacturing of drinking straws, as they allow for the production of straws with custom bends or curves to suit specific products or packaging requirements. They are also used in the production of novelty straws with unique shapes or designs.
![]() |
![]() |
Flexible straw |
Overall, a flexible straw bending machine is a specialized piece of equipment that helps to streamline the production process of straws and allows manufacturers to create a range of customized straw products.
Yinko dedicated to the development of high quality machines with competitve price, we are focusing on manufacturing the drinking straw making machines, paper cup machines, packing machines.
should you have any interest in our machines,please feel free to contact us.
The future of PLA biodegradable drinking straws is looking bright.
With the increasing awareness of plastic pollution and its effects on the environment, more and more people are turning to eco-friendly alternatives like PLA biodegradable drinking straws.
![]() |
![]() |
These straws are made from polylactic acid (PLA), a bioplastic derived from renewable resources like corn starch or sugarcane. Unlike traditional plastic straws, PLA straws are 100% compostable and biodegradable, making them an ideal choice for those looking to reduce their environmental impact. PLA straws offer a number of advantages over traditional plastic straws.
![]() |
They are lightweight, durable, and flexible, making them perfect for use in cold drinks like smoothies or milkshakes. They also don’t contain any toxins or chemicals that could leach into your drink. Plus, they come in a variety of colors and sizes so you can find the perfect fit for your needs.
The future of PLA biodegradable drinking straws looks promising as more companies begin to recognize their potential and start offering them as an alternative to traditional plastic straws.
As consumers become more aware of the environmental impacts of plastic pollution, they will likely continue to seek out eco-friendly options like PLA biodegradable drinking straws when purchasing food and beverages. This could lead to increased demand for these products in the coming years, creating new opportunities for businesses to capitalize on this growing trend.
Overall, PLA biodegradable drinking straws are a great way to reduce your environmental impact while still enjoying your favorite drinks without worry about toxins or chemicals leaching into them. As awareness continues to grow about the dangers of plastic pollution, we can expect to see an increase in demand for these eco-friendly alternatives in the near future.
As a one stop solution provider, we have dedicated to the development and manufacturing of PLA straw making machine for many years, the PLA straw making machine can works efficiently and smoothly, gives the super quality PLA straws. it can be your reliable partners in the drinking straw business.
![]() |
![]() |
if you are interested to set up the new production line or step into this industry, we'd like to provide our professional services to you. call us for a solution!
Trapezoidal screw: Pure sliding friction - brass (good self-lubrication) has a very low efficiency of 60%, a simple structure, low cost and no precision, large surface contact load, large starting resistance, resulting in creeping and creeping during ultra-low speed operation. Trapezoidal screws can be selected when there is no precision requirement, a large axial load is required, the budget is low and the cost needs to be reduced, the speed is low, and the occasion is not important.
Ball screw: It realizes high-efficiency and low-friction transmission through rolling media, with an efficiency of more than 90%. Compared with surface contact, ball is point contact, with smaller load, higher precision and higher cost.
The speed of the screw is limited, and it is best to control it within 1500rpm. If the screw is too long, it needs to be pressed down to within 1000rpm.
Unit movement of the screw: lead (pitch, Pb)
[Fixed seat]: Angular contact bearings are used in pairs to constrain the axial direction of the screw and are mainly used to bear the axial force of the screw
[Support seat]: Deep groove ball bearings are used alone, purely to support the tail of the screw, so that it does not run around and can slide axially
[Fixed + Support]: The most classic structure
[Fixed + Free]: There is no way to put it, there is no place to install the support seat (short stroke, structural requirements), the speed cannot be too high, and the load should not be too large
[Fixed + Fixed]: Not suitable for high-speed operation, heating will cause the screw to deform and get stuck, very good rigidity, high precision
[Support + Support]: No precision, loose mechanism, small load, almost no requirements for motion performance---hand-cranked adjustment mechanism
Nut structure of ball screw
[External circulation]: Better high-speed performance, complex structure, higher cost
[Internal circulation]: Slightly lower cost, more compact structure, easy to install
Ball Screw precision
C0 C1 .......C7 C10 ...
The larger the number, the worse the accuracy and the lower the cost
The screw rods of C7 and later are processed by extrusion molding --- rolled screw rods: high production efficiency----cheap, short delivery time
The screw rods of C5 and earlier are processed by whirlwind milling + grinding --- ground screw rods: low production efficiency---very expensive, high accuracy
The most used: C7
Ball Screw Preload
Effectively prevent the nut seat from offsetting due to clearance when the load is large (improve the dynamic accuracy of large loads)
Increases internal stress, greater resistance, and increased heat generation
EPE foam fruit net extrusion machine are becoming increasingly popular in India because of their efficiency, cost-effectiveness, and high-quality output. This article will cover the feedback from the Indian market, various applications of these machines, and their key advantages.
Our EPE foam fruit net extrusion machines have received positive feedback from Indian customers. Clients have particularly praised the machine's durability, low maintenance requirements, and high output rates. Many businesses in India, ranging from small-scale operations to large enterprises, have noted significant improvements in their production efficiency and product quality after integrating our machines into their processes.
The EPE foam fruit net extrusion machine has a wide range of applications and significant potential in the Indian market:
Agricultural Packaging: Primarily used for packaging export fruits like apples, pears, mangos, and grapes, providing protection during transportation and storage to maintain quality and reduce damage. This is particularly important for exports to markets such as the Middle East, Europe, and Southeast Asia.
Horticulture and Floriculture: Used to protect flowers and plants during transport, preventing damage to stems and leaves. This application is especially crucial for exporting floral products to countries like the USA, Netherlands, Germany, and Japan.